Why we need to use oil-resistant cables in industries?
In factories such as chemical processing plants, F&B factories, the oil and gas industry, etc., cables are often exposed to oil and chemicals due to leakage from equipment and machinery. Therefore, resistance to oil and chemicals is a requirement that these cables need to meet.
Nowadays, the requirements of the industrial environment are increasingly complex and up to date with new trends. For some special fields with harsh production environments, it is important to use electrical products and equipment with suitable properties and technical data, because this contributes to ensuring the stable operation of the factory system determined and effective. In particular, in factories such as chemical processing plants, F&B factories, the oil and gas industry, etc., cables are often exposed to oil and chemicals due to leakage from equipment and machinery. Therefore, resistance to oil and chemicals is a requirement that these cables need to meet.
Each industry has its own properties that require corresponding technical requirements. If in factories with high-temperature and flammable working environments, it is necessary to limit short-circuit or fire, fire-resistant and fire-retardant cables are the right choices to solve this problem. On the other hand, electric cables in production environments that use a lot of oil and cleaning chemicals will have to come into frequent contact with these substances. Therefore, if these cables do not have custom characteristics or designs, they will suffer from internal and external quality problems, adversely affecting the entire plant system.
Some effects when cables are exposed to oily and chemical environments for a long time such as:
- Cracking
When operating for a long time in an oily environment, the plastic in the cable will gradually be removed, making the insulation and outer sheath brittle, and fragile, and causing cracking.
- Swelling
The cable is immersed in the oil environment for a long time, and the oil will seep into the sheath, at this time the diameter of the insulation and protective sheath increases significantly, causing the cable to swell.
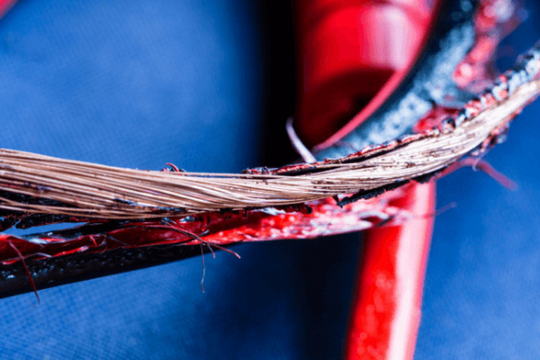
- Melting
Electric cables will be easily damaged and not as good as the original when the components are exposed to oil and chemicals for a long time, leading to melting.
- Discoloring
The plastic in the cable and the color in the sheath will be affected by oils and chemicals, causing fading in the power cable.
All four of the above phenomena cause negative effects on the cable, making the signal transmission unstable and reducing the plant's performance. It even causes a short circuit or a fire, causing the factory to stop production. For these reasons, in addition to regularly checking electrical systems and equipment for timely repair, you should choose cables with suitable properties, oil resistance, and chemical resistance to save money on the repair budget, and contribute to ensuring safety.
Oil-resistant cables have different designs and properties. In particular, the oil-resistant cables are announced through the attached product documentation of the manufacturer. Some basic information is mentioned such as oil type name, oil resistance level, attachment standard name (UL, Oil Res I, and Oil Res II), and many more parameters. Depending on the different properties of the production environment, we can adjust the design of the cable to best suit it, ensuring that the wire's technical requirements are compatible with the factory environment.
Some oil-resistant cables that you can refer to are:
- JZ-500 cables
The control cable series is resistant to oil and oil-based chemicals, is resistant to torsion, free of Cadmium, Silicone and free of harmful substances.
_any_large.jpg)
- F-CY-JZ cables
F-CY-JZ cable has an anti-interference layer of tinned copper mesh with 85% coverage, is resistant to oil and oil-based chemicals, is free of Cadmium, Silicone, and is free of harmful substances.
A special property of this line is that a plastic shield is added between the conductors and the tinned copper mesh, which does not damage the insulation, making the wire light and having a good bend radius.
- F-CY-JZ cables
F-CY-JZ cable has an anti-interference layer of tinned copper mesh with 85% coverage, is resistant to oil and oil-based chemicals, is free of Cadmium, Silicone, and is free of harmful substances.
A special property of this line is that a plastic shield is added between the conductors and the tinned copper mesh, which does not damage the insulation, making the wire light and having a good bend radius.
_any_large.jpg)
- Y-CY-JB cables
The cable has an anti-interference layer of tin-plated copper mesh with 85% coverage. The PVC sheath helps to increase mechanical stress, especially the transparent PVC cover highlights the optical visibility of the tin-plated copper anti-jamming mesh.
_any_large.jpg)
You can prioritize the selection of suitable cables depending on your needs and the environmental conditions in which the machine is manufactured. The above are suggestions for reference, if you need more advice and support for specific electrical connection solutions, please contact our engineers for advice and support!
For more information, please contact:
HELUKABEL® Vietnam
54, Street 1, Cityland, Ward 7, Go Vap District, Ho Chi Minh City 700000, Vietnam
Tel. +84 28 22536441 | info@helukabel.com.vn | www.helukabel.com.vn
SCHEDULE A MEETING WITH OUR ENGINEERS HERE !