Trench digging is out
A new technique from Herrenknecht promises to transport electricity generated by wind farms in Northern Germany to the south of the country underground, without spoiling the countryside.
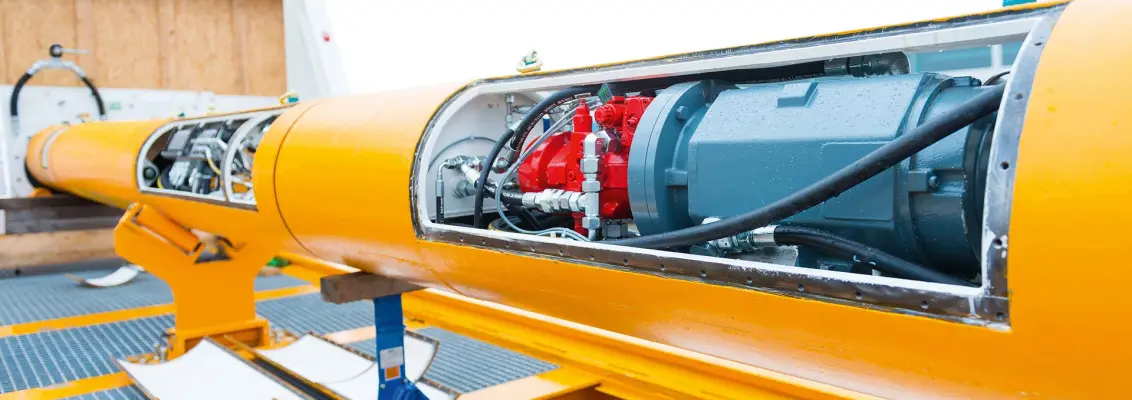
A new technique from Herrenknecht promises to transport electricity generated by wind farms in Northern Germany to the south of the country underground, without spoiling the countryside.
Berlin, 2nd July 2015: At the energy summit, the government coalition votes to expand power lines. One of the core decisions: the windpower electricity generated in the north of country should be transported to the south via new DC lines. And where possible, the 2,400 kilometres (1,491 miles) of high-voltage DC transmission lines should be laid underground.
Varel, 10th November 2017: Tobias Engel stands in mud as fine sleet falls on his helmet. It’s cold and inhospitable – and there’s a lot of activity going on around him. A nine-metre (30-foot)-long jacking pipe hanging from a crane is about to be lowered into the construction pit. “When this pipe is out of the way, we’ll have completed the second pipe run,” says Engel. He is Herrenknecht’s Utility Tunnelling R&D project manager. Based in Schwanau on the edge of the Black Forest, the company is best known for its impressively large tunnel boring machines. Together with his colleagues, Engel has developed a technique that seems unimpressive at first glance: E-Power Pipe®. This concept makes the Berlin government representatives’ resolution to lay power lines underground feasible. It’s also the reason Engel is currently standing in the middle of a construction site in Lower Saxony, for here is where E-Power Pipe® is being put to use for the first time since its market launch.
“We can now bore distances of 1,000 metres in one go.”
-Tobias Engel, Herrenknecht’s Utility Tunnelling R&D project manager
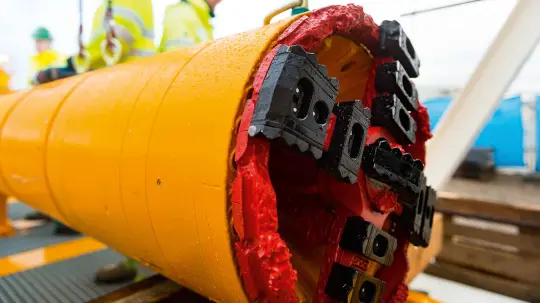
DOWN AND AWAY INTO THE GROUND
Walking around the building site, Engel explains why E-Power Pipe® is so revolutionary: “With the conventional cut-and-cover technique, a 45-metre (148-foot)-wide strip of top soil has to first be removed, followed by the soil layers of the corresponding ditch profile. Each layer has to be stored in a separate pile and shovelled back afterwards in the same order when the work is complete. This makes it an extremely cost-intensive process with a huge impact on nature,” he explains. In particular, densely populated areas and route sections with many physical obstacles such as residential neighbourhoods, protected water and nature reserves, and military land pose challenges to the planners.
Up to now, there has been no alternative as the cables have to be laid just below ground, a specific distance apart, and as accurately as possible over long distances. All previous trenchless solutions for under-ground cables have failed due to cost, safety, and time issues. E-Power Pipe® is expected to change this. “We’re now able to achieve pipe runs exceeding 1,000 metres (3,280 feet). This means we can bore this distance all at once at a depth of just 1.5 metres (5 feet) below ground.
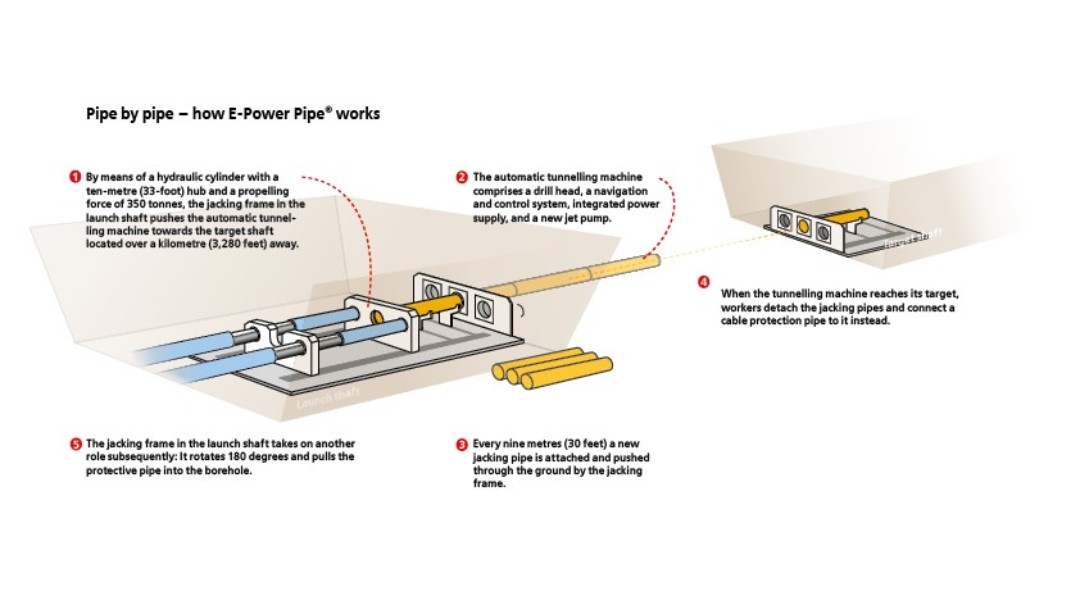
Schwanau, 10th November 2017: When he looks out of his office window, Stefan Pabst sees meadows, fields and overhead power lines. The latter should start disappearing from the landscape in the future thanks to his work. Stefan Pabst is the process engineering manager for Utility Tunnelling at Herrenknecht. Along with his colleague, Michael Huser, he has equipped the tunnelling machine with the electronics and software needed for the new technique. This was no easy feat as its outer diameter of 490 millimetres (19 inches) left little room for the required components. “The lack of space for the power supply and data communication was a headache too. We had to fit both into a single cable with a diameter less than 70 millimetres (3 inches),” recalls Pabst. Separate cables were out of the question: “When the new jacking pipes are installed, quick and easy cable-coupling is a must. It takes about twelve minutes to push a pipe forward, and if coupling takes too long, we lose the benefit of our good tunnelling time. Two cables would be too cumbersome. What we needed was a single, multipurpose cable,” says Pabst. But an off-the-shelf solution didn’t exist. So he contacted Rainer Maier, HELUKABEL’s regional sales manager: “I told him we needed a cable capable of transmitting 22 kilowatts at 690 volts, and that it had to include a data cable as well,” explains Pabst. Not an easy task: “The challenge of carrying energy, equivalent to the amount used to power two homes, via an extremely small cable over a distance of 1,500 metres (4,921 feet) is no straightforward matter,” he notes.
MAXIMUM POWER, MINIMUM DIAMETER
Rainer Maier knew immediately that a hybrid cable for the power and data transmission was the solution. “The wealth of experience gained from previous joint projects made the task easier for our development experts in Windsbach,” he says. With the focus on a small diameter, the team got down to work and soon presented Stefan Pabst and Michael Huser with a first suggestion: a 25 square millimetre (4 AWG) cross-sectional power supply cable. “But then specifications changed and more power was needed which is why the present cable now has a cross section of 35 square millimetres (2 AWG). Through the intelligent layout of the various components, we were able to further reduce the diameter,” reports Maier. This greatly helped Herrenknecht with the design of the connector says Stefan Pabst: “As this takes up even more space, the small cable diameter was essential to keep the connector’s diameter below the maximum 70 millimetres (3 inches).
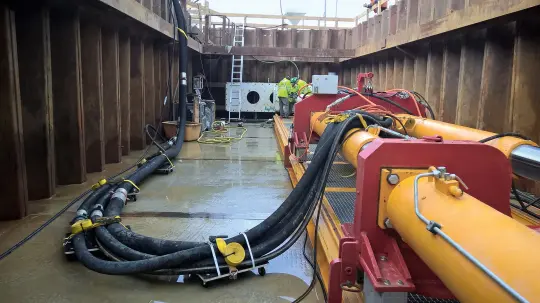
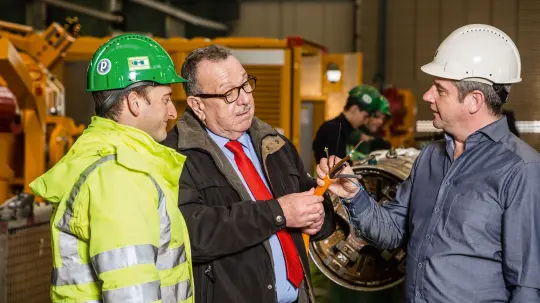
TWO PLUS THREE
The development partners also proceeded step by step with the component design of the data transmission cable. “Initially we intended to have two data conductors,” explains Herrenknecht’s electronics engineer, Michael Huser. “One for navigation and one for control. However, when we realised we needed even more precise tunnelling-machine control, we had to add a second navigation system which meant an additional conductor pair for the CAN bus.” The Windsbach experts made this possible by creating an impressive complete package containing a five-component, small-diameter cable for voltages between 375 and 690 volts. Today, the HELUKABEL solution powers the two navigation systems, the control unit and the drill head, while ensuring reliable data communication between the machine and control console. Huser and Pabst are satisfied along with their colleague Tobias Engel in Varel. There, the jacking frame is already retracting the cable protection tube. Another section of the southbound route has just been completed.
THE TUNNEL EXPERTS
Who: Herrenknecht AG, Schwanau, with approx. 5,000 employees.
What: Herrenknecht is a leading manufacturer of tunnelling machines for all diameters and the broadest diversity of geologies. The machines are used in a variety of applications including railway, metro, road, utility, pipelines, hydropower, mining and exploration.