Single core vs multicore cables: What are the differences?
Single core cables are composed of a single copper conductor, while multi core cables consist of multiple smaller strands twisted together for greater flexibility, making them suitable for complex structures. The choice between single core and multi core cables depends on the specific requirements of each electrical project, as each type offers unique advantages.
Contents:
1. Advantages and disadvantages of single core cables
2. Advantages and disadvantages of multicore cables
3. Comparing single core cables and multicore cables
4. Top 60+ HELUKABEL's single core cables
1. Single core cables
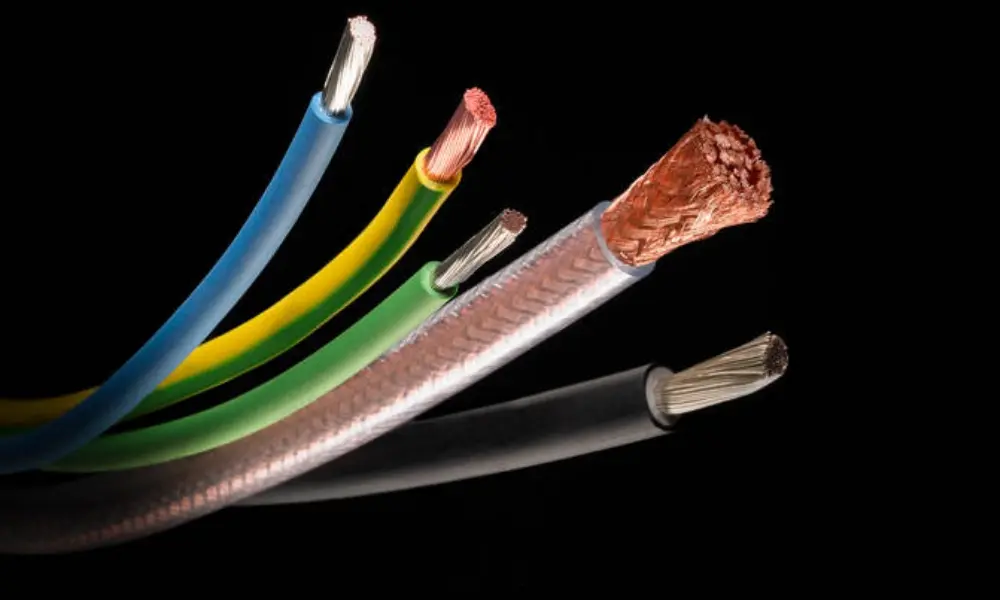
Single core cables
1.1 What are single core cables
Single core cables consist of a single electrical conductor covered in an insulating layer. This type of cable is more robust compared to multi core cables. Its sturdy and cost-effective design allows it to withstand harsh environmental conditions. Single core cables are commonly used in outdoor environments, vehicle control systems, electrical conductors, and construction projects to transmit high currents.
>>See more: Classification of single core cables
1.2 Advantages of single core cables
Single core cables offer the following advantages:
- Single conductor design: With a single conductor, single core cables ensure flawless connectivity and termination. This minimizes the risk of disconnection and guarantees optimal performance in electrical systems.
- High current-carrying capacity: Single core cables can handle higher currents as there are no gaps between the conductors. For the same cross-sectional area, single core cables have a higher density of conductive material, enhancing electrical transmission efficiency.
- Superior durability and corrosion resistance: The solid structure of single core cables provides exceptional durability. The corrosion-resistant properties of copper or aluminum materials enable these cables to perform reliably in harsh conditions, whether indoors or outdoors.
- Low voltage drop: Single core cables have lower electrical resistance compared to multi core cables, leading to reduced voltage drops along the circuit. This is particularly beneficial for long-distance electrical transmission, minimizing energy losses.
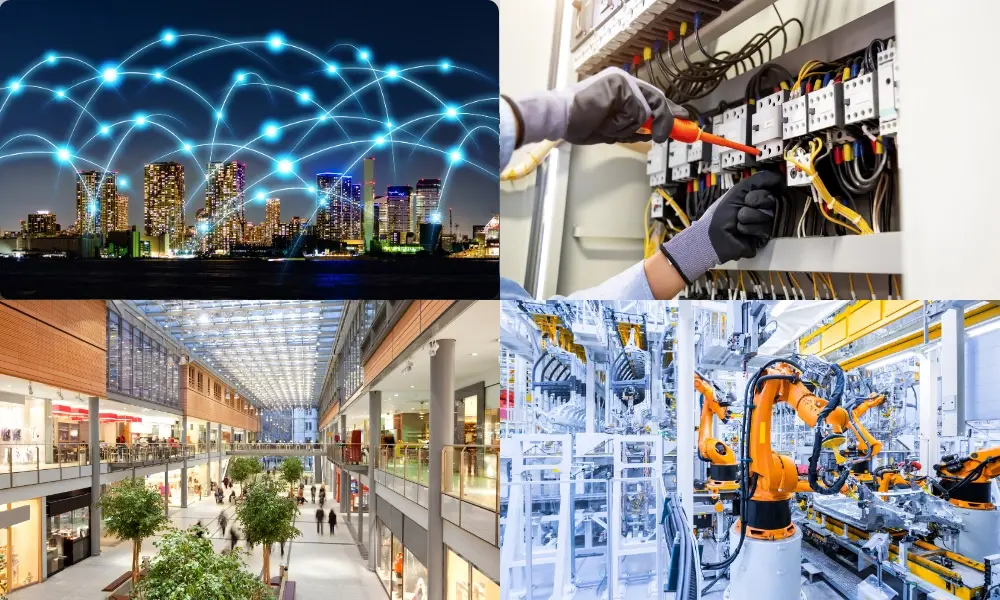
1.3 Disadvantages of single core cables
- Lack of flexibility: Single core cables are stiffer and harder to bend compared to multi core cables. This makes them unsuitable for applications requiring high flexibility, such moving applications or situations that demand frequent bending.
- Susceptible to damage in repetitive motion applications: In environments with continuous motion or strong vibrations, single core cables are prone to cracking or breaking as they cannot withstand repeated mechanical stress. For such specialized applications, users should opt for single core cables with enhanced mechanical properties, such as anti-twist or abrasion-resistant designs.
- Skin effect: In high-voltage or high-frequency applications, the skin effect can cause current to concentrate on the conductor's surface, reducing efficiency.
1.4 Applications of single core cables
Some prominent applications of single core cables include:
- Household electrical appliances
- Residential electrical systems
- Control panels and industrial automation systems
- Telecommunication systems
2. Multicore cables
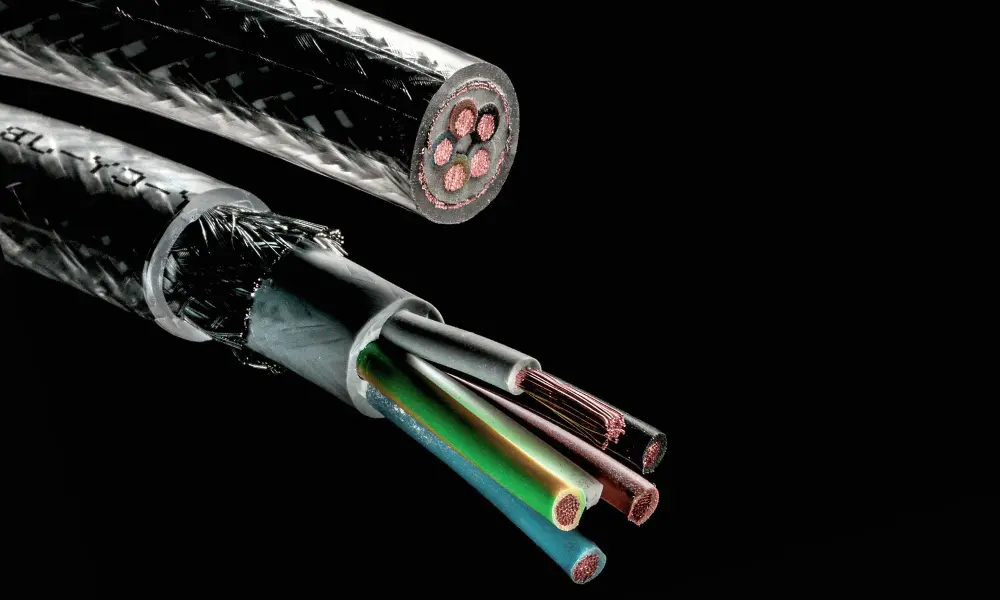
2.1 What are multicore cables?
Multicore cables are a popular choice in electrical applications due to their superior flexibility compared to single core cables. Comprising multiple small metal strands twisted or braided together, multicore cables offer durability and perform well in environments that demand frequent movement or bending.
2.2 Advantages of multicore cables
- High flexibility: Compared to single core cables, multicore cables are easier to bend, twist, and adjust, making them an ideal choice for applications requiring movement or installation through electrical conduits within walls. These cables are especially suitable for applications involving repetitive motion.
- Safe electrical conduction: The spaces between the strands allow electricity to flow through multicore cables more safely while reducing the amount of heat generated during current transmission. This ensures stable performance, even in high-current applications.
- Reduced skin effect: In alternating current (AC) systems, multicore cables are preferred to minimize the skin effect - a phenomenon where the current concentrates on the surface of the conductor, leading to energy loss.
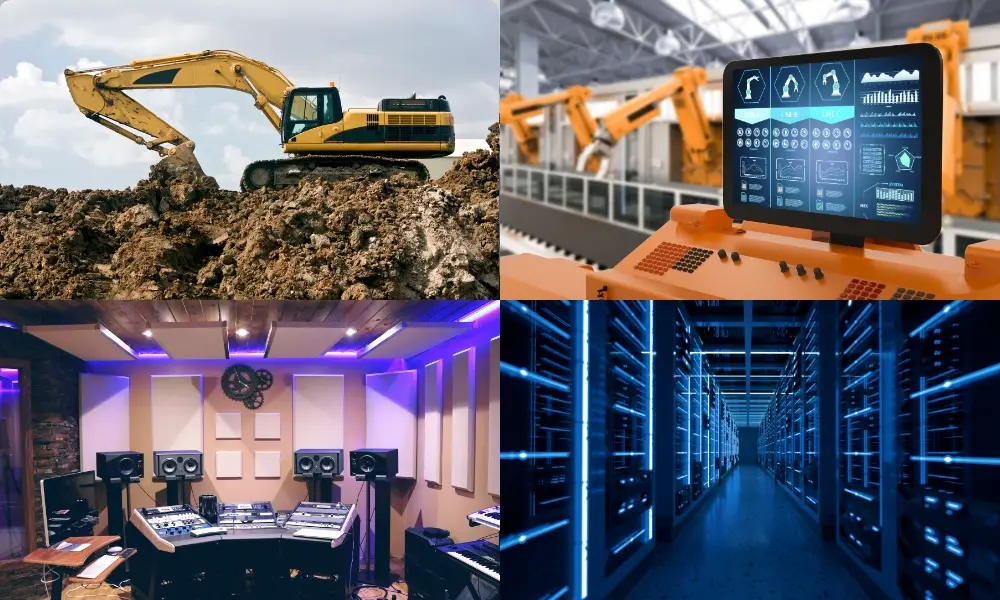
2.3 Disadvantages of multicore cables
- Higher corrosion risk: Multicore cables are more prone to corrosion, particularly in humid or outdoor environments. This can reduce their conductivity and lifespan. To mitigate this, users should opt for high-quality insulation materials like PUR, TPE, or rubber.
- Lower ampacity: The gaps between the strands in multicore cables result in a lower current-carrying capacity compared to single core cables of the same cross-sectional area. This factor should be considered when designing electrical systems that require high currents.
- Higher voltage drop: Multicore cables may experience greater voltage drops over long distances, which can impact efficiency. In high-frequency communication applications, multicore cables can also introduce signal interference, with attenuation rates ranging from 20-50%.
2.4 Applications of multicore cables
Some typical applications of multicore cables include:
- Power supply for heavy-duty industrial machinery
- Connection of electronic devices and audio applications
- Data transmission applications such as data centers, office networks, telecommunications…
3. Comparing single core cables and multicore cables
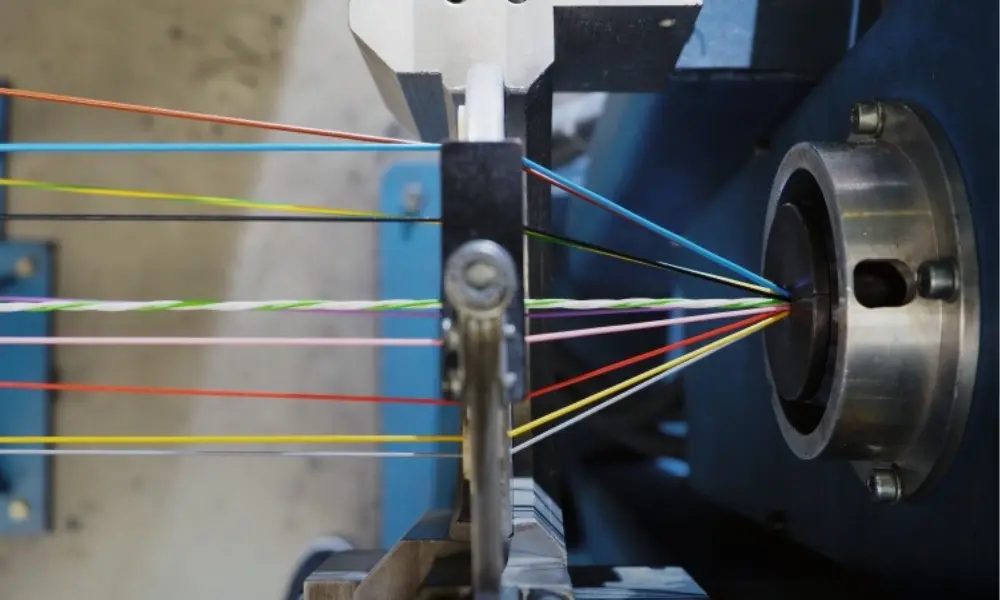
3.1 Durability and flexibility of single core and multicore cables
Single core cables are more durable and robust, making them suitable for applications requiring high tensile strength and long-term stability. However, their stiffness makes them less flexible and not ideal for applications involving frequent bending or movement.
On the other hand, multicore cables, made from multiple smaller strands twisted together, offer higher flexibility but have lower mechanical strength compared to single core cables. This flexibility makes multicore cables easier to install and route in tight spaces.
3.2 Electrical conductivity performance
Single core cables provide more stable and efficient current transmission across a wide frequency range. Due to their solid structure, they are less affected by external factors such as vibrations or corrosion. With a thicker core, single core cables have a smaller surface area, which reduces energy loss.
In contrast, multicore cables, with their twisted strands and air gaps, have a larger surface area and therefore consume more energy. For long-distance applications, single core cables are the optimal choice due to their ability to minimize current loss. Multicore cables, however, perform better in short-distance applications.
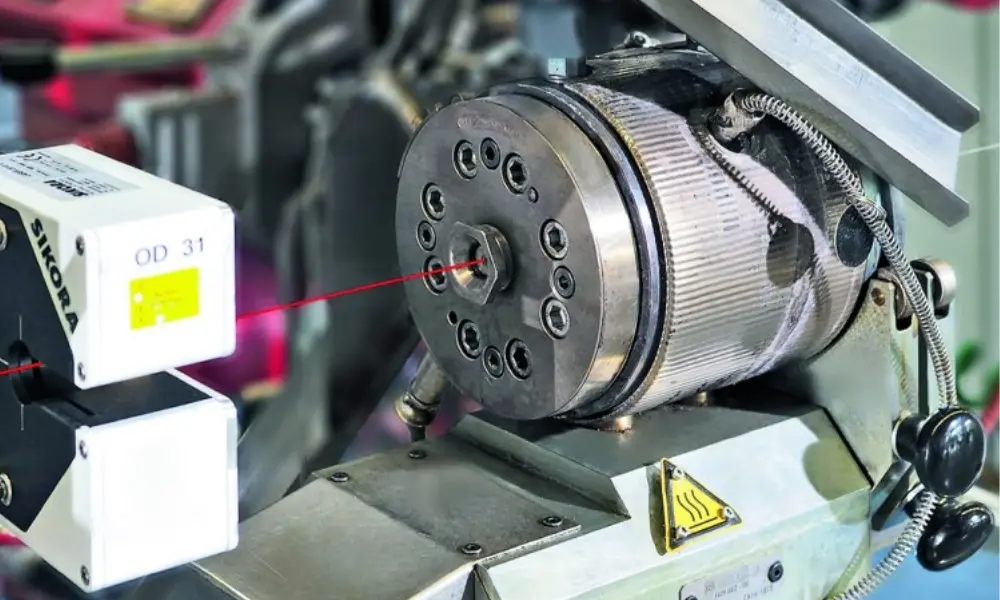
Cable manufacturing process of single core cables and multicore cables
3.3 The more complex manufacturing process of multicore cables
The production of single core cables begins with drawing copper rods through a series of progressively smaller molds to achieve the desired size for each application. This drawing process makes the copper thinner and more brittle. The copper wire is then annealed by heating to improve its strength and ductility. Finally, the wire is finished either as bare copper or insulated for use.
The production of multicore cables is a more complex process, requiring a combination of precision engineering and advanced technology. The multicore cables manufacturing process involves several stages, including the drawing and annealing of individual copper strands. These strands are then twisted around a central core with the help of specialized machinery. The complexity of this multi-core production process results in higher costs compared to single core cables.
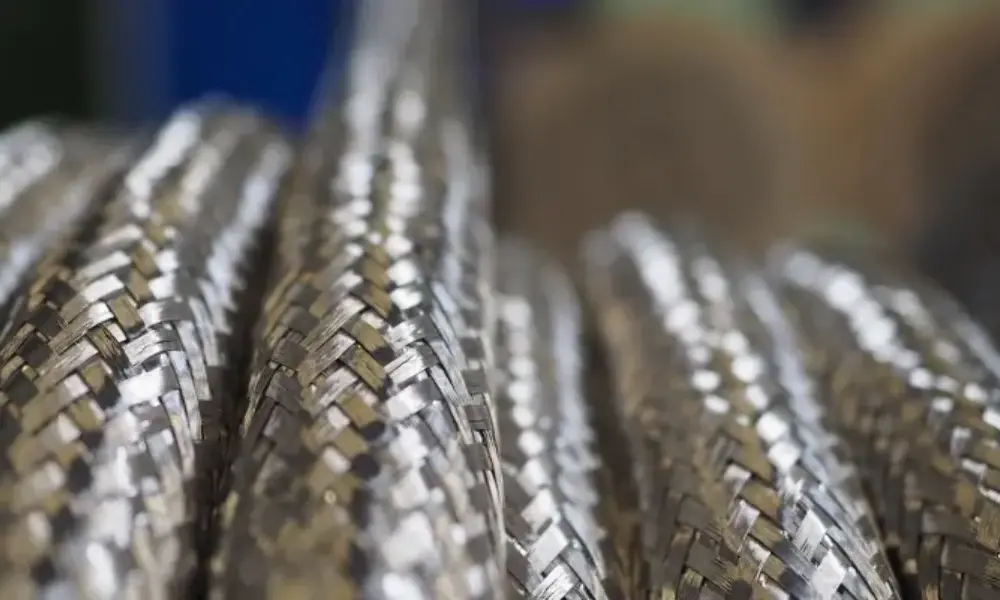
A braided C screen cable with tinned copper mesh provides coverage exceeding 85 per cent
3.4 Higher current-carrying capacity of single core cables
Although both single core and multicore cables have the same cross-sectional area, single core cables can carry higher currents and have lower resistance due to their smaller surface area.
Multicore cables, with their larger surface area, typically result in higher voltage drop over long distances. However, the air gaps between the strands in multicore cables allow for better heat dissipation, making them suitable for applications requiring quick thermal management.
3.5 Corrosion resistance
Single core cables generally have better corrosion resistance than braided wires due to their solid structure, which has fewer gaps for corrosion to develop. In contrast, multicore cables with multiple smaller strands and air gaps are more susceptible to corrosion, especially in humid or outdoor environments. However, multicore cables can be tinned to reduce the risk of corrosion and extend their lifespan.
4. Top 60+ HELUKABEL’s single core cables
HELUKABEL's product range of single core cables include a variety of options, made from different materials (PVC, PUR, rubber, silicone…) with various characteristics (halogen-free, temperature-resistant), making them suitable for a wide range of applications, including solar energy, continuous motion applications, and automotive industry.
1. H05V-K / 05V-K 2. H07V-K / 07V-K 3. FIVENORM H05V2-K / 05V2-K 4. HELUKABEL® SINGLE CORE UL Style 1015 5. LiYv 6. LifY 7. HELUKABEL® SINGLE CORE UL Style 1007 8. Single 600-J / Single 600-O 9. H05V-U 10. Single 602-RC-J / Single 602-RC-O 11. HELUKABEL® SINGLE CORE UL Style 1569 12. PVC H07V-U 13. Single 602-RC-CY-J / Single 602-RC-CY-O 14. H07V-R 15. Single 600-CY-J / Single 600-CY-O 16. FIVENORM H07V2-K / 07V2-K / H07V-K / 07V-K 17. HELUWIND® WK POWERLINE ALU 1,8/3 kV 18. MULTISPEED®-600-PUR-J / MULTISPEED®-600-PUR-O 19. MULTISPEED®-600-C-PUR-J / MULTISPEED®-600-C-PUR-O 20. HELUWIND® WK POWERLINE ALU ROBUST 0,6/1 kV 21. SiF 22. SiFF 23. SiD 24. SiD/GL 25. SiF/GL 26. HELUKABEL® SINGLE CORE UL Style 3135 27. HELUTHERM® SINGLE CORE UL STYLE 3512 28. NSGAFÖU 1,8/3 kV 29. H01N2-D 30. NSHXAFÖ 1,8/3 kV | 31. H07G-K / 07G-K 32. H01N2-E 33. H05G-K 34. H07Z-K / 07Z-K 35. HELUTHERM® 145 36. H05Z-K 37. HELUTHERM® 145 UL/CSA 600V 38. HELUTHERM® 400 39. HELUTHERM® 145 UL/CSA 300V 40. HELUKABEL® SINGLE CORE UL Style 3135 41. HELUPOWER® THERMFLEX® 145-Single 42. HELUPOWER® THERMFLEX® 145 43. HELUTHERM® SINGLE CORE UL STYLE 3512 44. HELUFLON®-FEP-6Y 45. HELUFLON®-PTFE-5Y 46. HELUTHERM® 600 47. HELUTHERM® 600-ES 48. HELUKABEL® SINGLE CORE UL Style 1015 49. HELUKABEL® SINGLE CORE UL Style 1007 50. THHN / THWN 51. KOMPOSPEED® 600 52. KOMPOSPEED® 600-C 53. Vehicle Cable FLRY 54. Vehicle Cable FLY 55. SOLARFLEX®-X H1Z2Z2-K NTS 56. HELUPOWER® SOLARFLEX®-X H1Z2Z2-K UL 57. HELUPOWER® SOLARFLEX®-X PREMIUM 58. SOLARFLEX®-X H1Z2Z2-K 59. ESUY 60. ESY 61. HELUPOWER® CU-CONDUCTOR-CL2 TINNED 62. HELUPOWER® CU-CONDUCTOR-CL5 TINNED |
If you still have any concerns or questions, don't hesitate to reach out to HELUKABEL Vietnam's engineering team promptly for detailed assistance.
HELUKABEL® Vietnam
Address | 905, Nguyen Kiem Street, Ward 3, Go Vap District, Ho Chi Minh City 700000, Vietnam |
info@helukabel.com.vn | |
Hotline | +84 28 77755578 |
Website | www.helukabel.com.vn |
Discover our products and place orders | Tiki | Product finder |
Follow us on | Facebook | LinkedIn | Instagram | Youtube | Zalo | WhatsApp | Tiktok | Spotify |