Features of single core cables for wind applications
Single core cables for the wind power industry need to meet anti-twist and oil resistance standards, ensuring accurate signal transmission.
Along with hydropower and solar power, wind power has rapidly developed and has become one of the renewable energy sources with significant growth potential. Wind turbines with large blades rotate steadily in the wind, converting mechanical energy into electrical energy. Inside the wind turbines is a complex system of electrical cables that play a crucial role in transmitting the generated electricity from the turbines to the grid.
1. Basic components of wind turbine
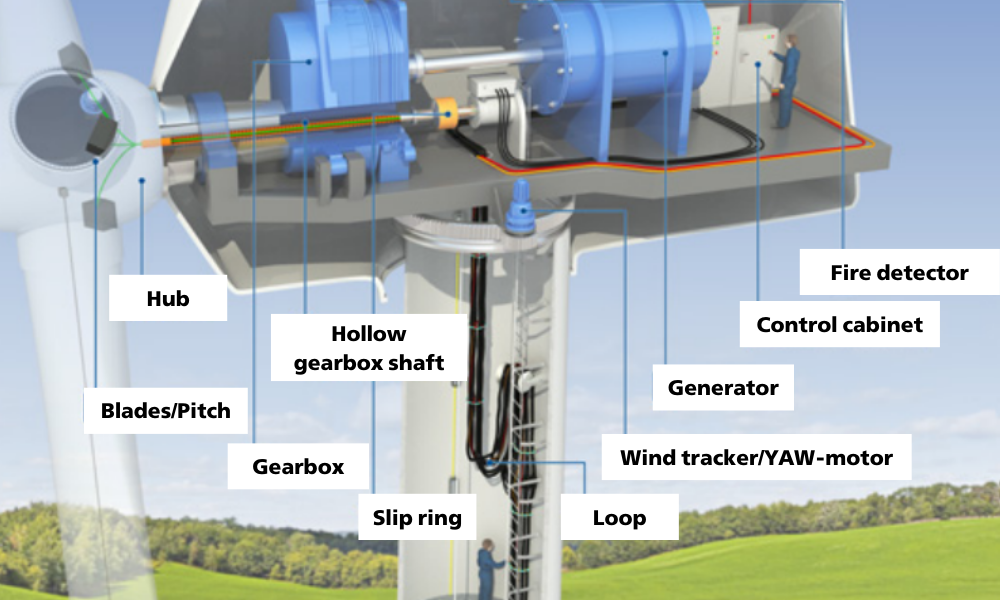
Some basic components of a wind turbine are as follows:
1.1 Nacelle
The nacelle houses the key components that convert the kinetic energy of the wind into mechanical energy to generate electricity. It is mounted on top of a tall steel or concrete tower, which can be up to 50 ft tall and weigh up to 300 tons or more, depending on the manufacturer and rated capacity.
The blades are essential components of a wind turbine, capturing wind energy and converting it into kinetic energy in the hub. The rotor, which consists of the blades, plays a vital role in generating electricity.
The hub is the center of the rotor, where the rotor blades are attached. Typically made of cast iron or steel, the hub redirects the energy from the blades to the generator.
1.2 Loop
In a wind turbine, a "loop" typically refers to the loops of cables or wiring systems designed to provide enough length and flexibility as the turbine operates. As the turbine blades rotate and other components move, the cables need to be able to stretch or shift to avoid being overly strained or damaged. These loops are often arranged in areas like the nacelle (the housing for the engine) or the tower of the turbine to ensure that the cables remain stable and safe throughout the turbine's operation.
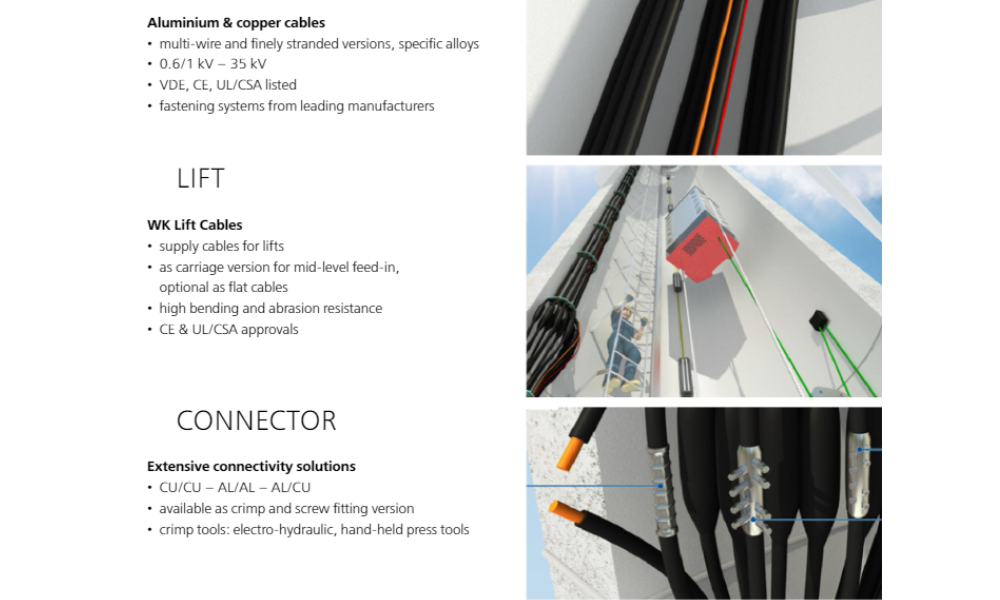
1.3 Wind tower and base
The wind tower supports the nacelle and is typically made of steel. The taller the tower, the more wind energy can be captured, resulting in greater electricity generation. The base stabilizes the wind turbine, anchoring it securely to the ground.
1.4 Lift
During installation, repair, and maintenance, all operations occur within the wind tower. As a result, most wind turbines are equipped with additional corridors and elevators to transport spare parts and small tools into the nacelle.
1.5 Connectors
The complex design of wind turbines necessitates a variety of cables to perform different functions. To fasten the installation and maintenance of turbine systems, designers are increasingly adopting "plug and play" solutions. The objective is to enhance the ease of installing and maintaining cable systems, thereby accelerating and simplifying the overall process of wind power system installation and maintenance.
2. Why are single core cables used for wind turbine applications?
Powering the motor of a wind turbine requires a robust power cable capable of withstanding environmental challenges and mechanical stresses, such as high winds, UV exposure, and salt spray. The movement of the blades and motor generates torque on various components, including the cable, so it is crucial to consider both the torsional and tensile stresses when selecting the power cable. The dynamic parts of the turbine further emphasize the importance of choosing the right cable.
In general, single core cables are relatively stiff and less prone to oxidation during use, offering a long service life. Although they consist of only one conductive core, single core cables are well-suited for installations involving multiple bends, corners, and twists.
>>See more: A glance at single core cables
3. What criteria must single core cables used for wind power applications meet?
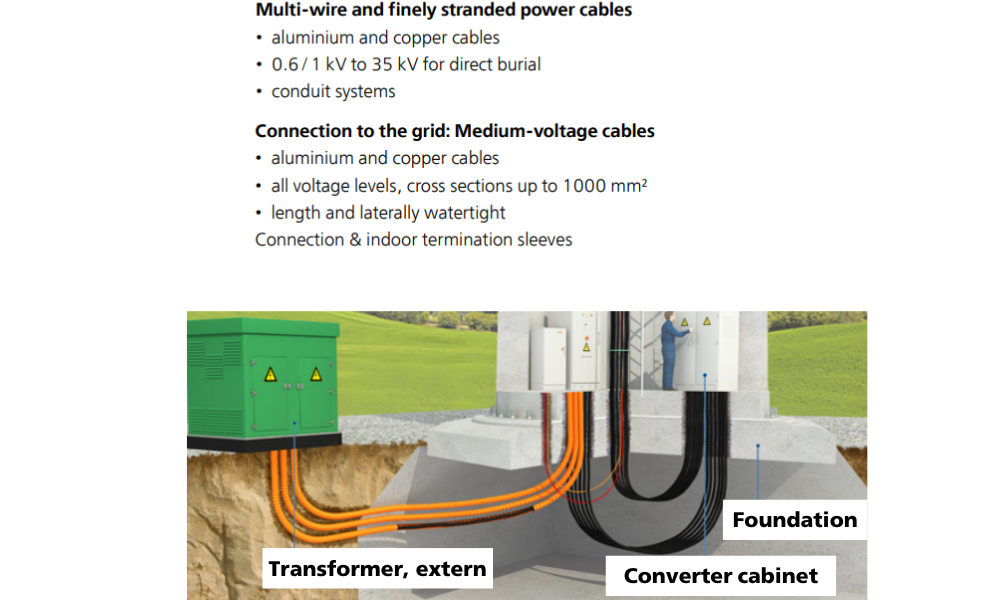
Single core cables are used in nacelles, generators, and wind towers
3.1 Abrasion resistance
In wind turbine systems, single core cables are used in nacelles, generators, and wind towers. The twisting motion during turbine operation can wear down the cable's outer layer, leading to insulation damage and eventually affecting the copper conductors. Therefore, single core cables used in wind turbines need to be made of thermoplastic elastomer or PUR materials, offering enhanced protection for the cables. Additionally, the outer layer of the single wire should have low adhesion to ensure that the cables can slide smoothly against one another.
3.2 High-temperature resistance
Wind turbines are installed in diverse environments: on land, offshore, or in high-altitude areas - often operating in extreme temperatures with wide temperature fluctuations. Certain single core cables are made from specialized synthetic materials that can function effectively in a temperature range from -55°C to +145°C.
3.3 Torsion resistance
In wind turbines, power cables are arranged in a loop to allow the nacelle and blades to rotate into the optimal position based on wind direction. This setup ensures stable power and data transmission even as the blades and nacelle move or rotate. The single core cables used in this loop configuration must be capable of twisting up to three times around their axis.
To ensure compatibility and durability, the WK series single core cables have undergone rigorous testing:
- Tested for more than 15.000 torsion cycles
- For climate zone from -40°C to +145°C
- Oil, ozone, and uv-resistant
- Multiple approvals available
- Cable grip
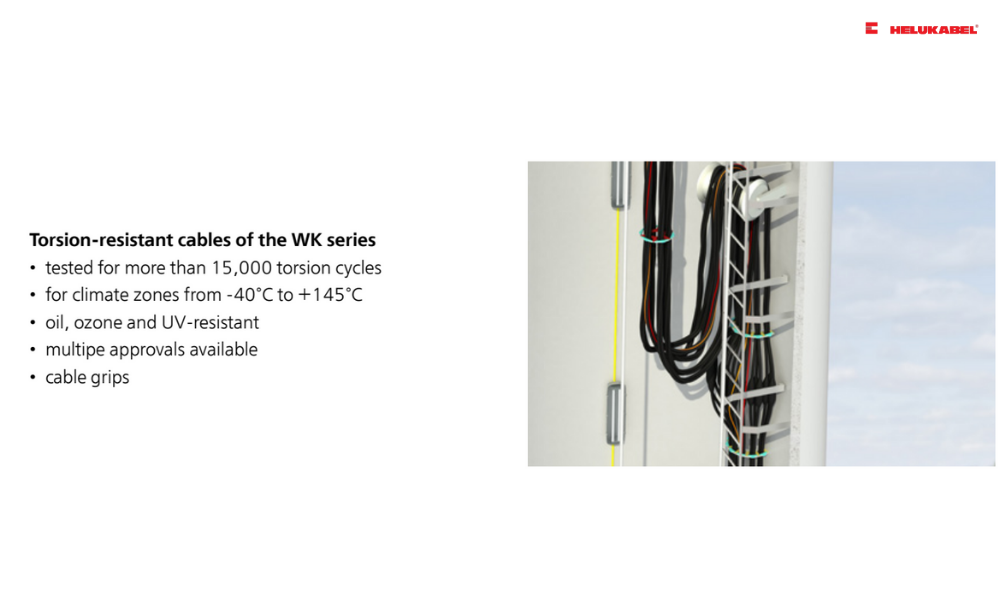
3.4 Oil resistance
Many mechanical components in wind turbines, such as gearboxes, bearings, and control systems, require lubricating and hydraulic oils to function. These oils can leak or spread to surrounding areas, coming into direct contact with the power cables. Prolonged exposure to oil can weaken, crack, or harden the cable sheath, leading to cable failure, safety risks, and reduced lifespan of the cables. To address this, HELUWIND WK single wire products undergo extensive testing for long-term durability, beyond the standard VDE or UL testing procedures (Oil Res I, Oil Res II).
3.5 Single core cables need to be halogen-free
Some wind turbines are installed in remote or offshore locations where access for maintenance and troubleshooting is difficult. In case of fire, a halogen-free cable system can limit fire spread, protect the electrical system, and reduce risks to people and equipment. Additionally, halogen gases can form acids when exposed to moisture in the air, causing corrosion of metal components and damage to surrounding systems. In wind turbines, this is especially critical as the electrical and control systems need protection from corrosive effects, thereby enhancing the lifespan and reliability of the equipment.
>>Find out more: HELUKABEL's portfolio of single core cables
4. HELUKABEL’s solutions for wind energy
With an abundant product portfolio, HELUKABEL offers optimal solutions for onshore and offshore wind turbines, as well as wind farms.
4.1 HELUWIND® WK POWERLINE ALU single core cables
HELUWIND® WK POWERLINE ALU single core cables are available with many versions:
Operating temperature (Flexing, fixed installation) | Minimum bending radius (Flexing, fixed installation) | Outer sheath material | Cross-section range | |
0,6/1 kV | -20°C to +90°C, -40°C to +90°C | 10x Outer-Ø, 4x Outer-Ø | Special PVC | 70 – 400 mm2 |
ROBUST 0,6/1 kV | -20°C to +90°C, -40°C to +90°C | 10x Outer-Ø, 4x Outer-Ø | Special PUR | 70 – 400 mm2 |
1,8/3 kV | -20°C to +90°C, -40°C to +90°C | 10x Outer-Ø, 4x Outer-Ø | Special PVC | 185 – 400 mm2 |
ROBUST 1,8/3 kV | -20°C to +90°C, -40°C to +90°C | 10x Outer-Ø, 4x Outer-Ø | Special PUR | 185 – 400 mm2 |
HALOGEN-FREE 1,8/3 kV | -20°C to +90°C, -40°C to +90°C | 10x Outer-Ø, 4x Outer-Ø | TPE-O halogen-free | 185 – 400 mm2 |
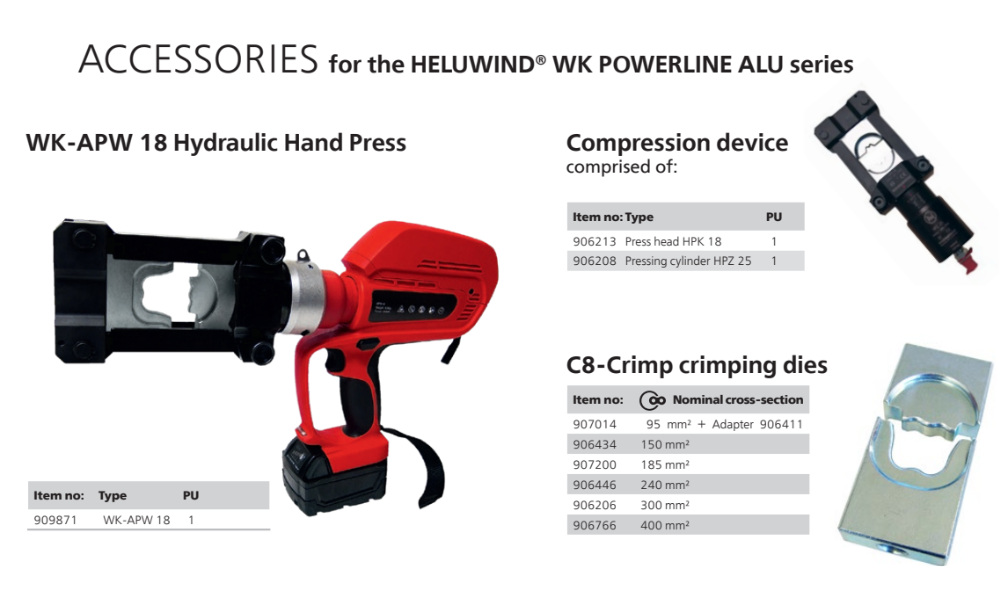
Various versions of the HELUWIND® WK POWERLINE ALU single core cables are suitable for a wide range of energy and plant engineering applications. Due to their high flexibility and low weight, installation times on-site can be significantly reduced. HELUWIND® WK POWERLINE ALU products can only be processed using the HELUKABEL® C8 crimping method, which is certified according to IEC 61238-1 Class A. Notably, the 1.8/3 kV version is suitable for direct burial, while the ROBUST version offers high resistance to abrasion and mechanical stress.
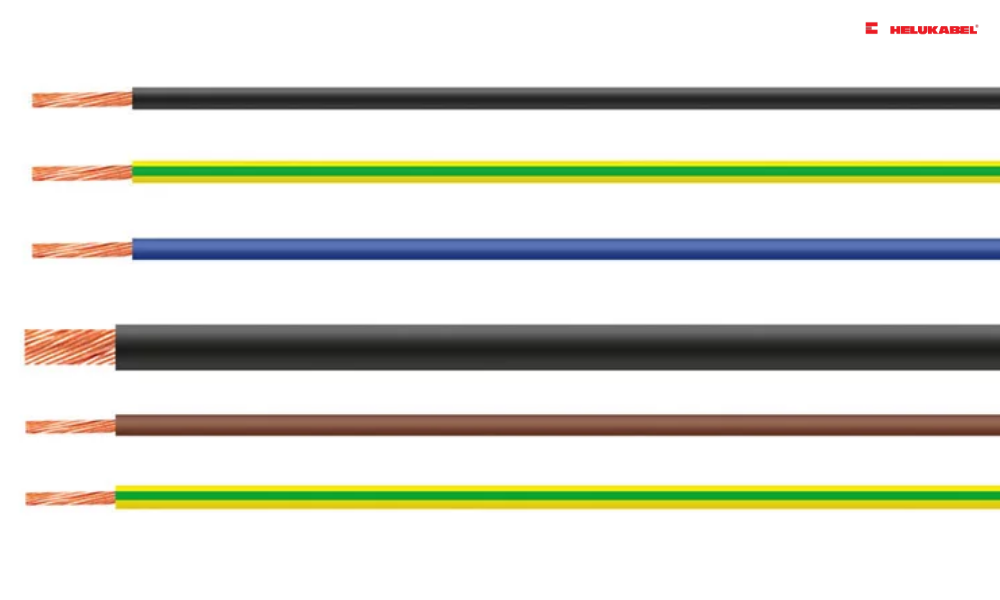
4.2 H05Z-K and H07Z-K / 07Z-K single core cables
These are two single core cables that are halogen-free, flame-retardant, ozone-resistant, and suitable for applications that require low smoke and corrosive gas emissions in the event of a fire. In addition, these two types of cables come in a variety of colors and cross-sections, making it easy for users to distinguish between wire types according to function such as phase wire, neutral wire, earthing wire, etc.
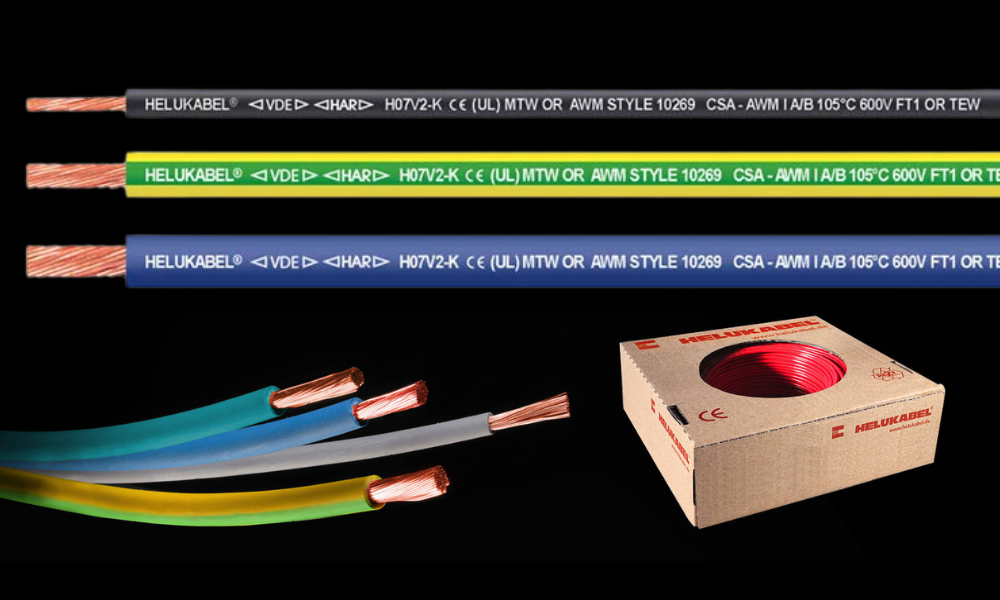
4.3 FIVENORM H07V2-K / 07V2-K / H07V-K / 07V-K single core cables
FIVENORM single core cables meet popular quality standards such as HAR - UL AWM - UL MTW - CSA AWM - CSA TEW, suitable for use worldwide. In addition, this cable line also has many color options, cross-section ranges from 1.5 - 150 mm2, voltage range up to 1000 V (AC) and 1250 V (DC).
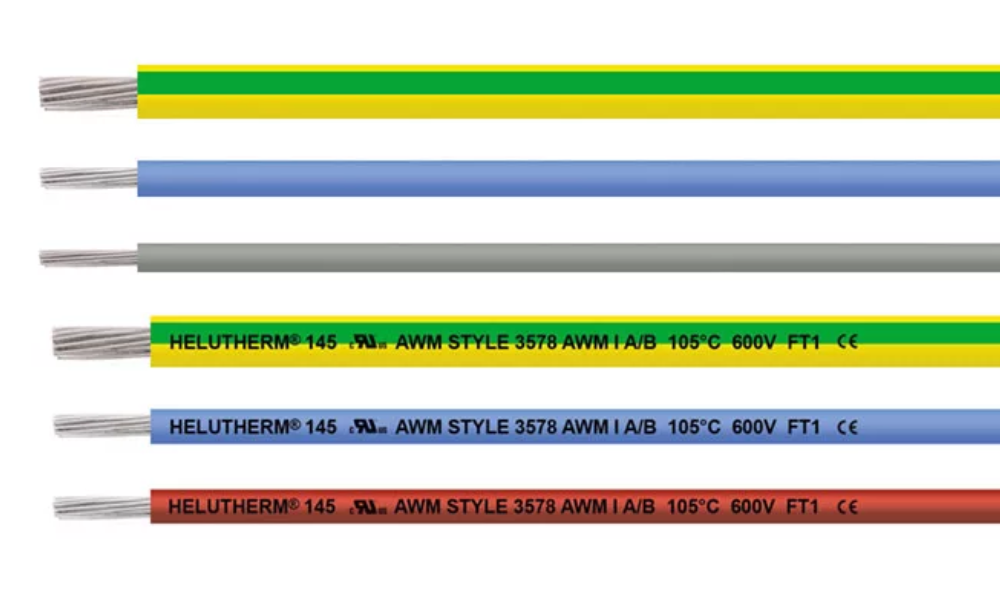
4.4 HELUTHERM® 145 and HELUTHERM® 145 UL/CSA 600V single core cables
HELUTHERM® 145 and HELUTHERM® 145 UL/CSA 600V single conductors have an operating temperature range of -35°C to +120°C (moving applications) and -55°C to +145°C (fixed installations). Available in a wide range of colors and cross sections, these are two heat-resistant single conductors for lighting, heating, electrical machinery, switching systems and distribution units in industrial equipment as well as building plant and machinery; suitable for installation in conduits, above and below plasterboard, in closed ducts, as well as for traffic systems and outdoor applications.
If you still have any concerns or questions, don't hesitate to reach out to HELUKABEL Vietnam's engineering team promptly for detailed assistance.
HELUKABEL® Vietnam
905, Nguyen Kiem Street, Ward 3, Go Vap District, Ho Chi Minh City 700000, Vietnam
Tel. +84 28 77755578 | info@helukabel.com.vn | www.helukabel.com.vn