What are robotic arms and their applications in industrial settings?
Robotic arms not only help automate processes in factories but also accelerate production and improve labor productivity. Let's explore the different types of robotic arms and their common applications in the following article!
Contents:
1. What are robotic arms?
2. Components and operating principles of robotic arms
3. Types of robotic arms
4. Applications of robotic arsm
5. Types of cables used in robotic arms
ROBOFLEX® cable series
Ethernet cables and BUS cables
1. What are robotic arms?
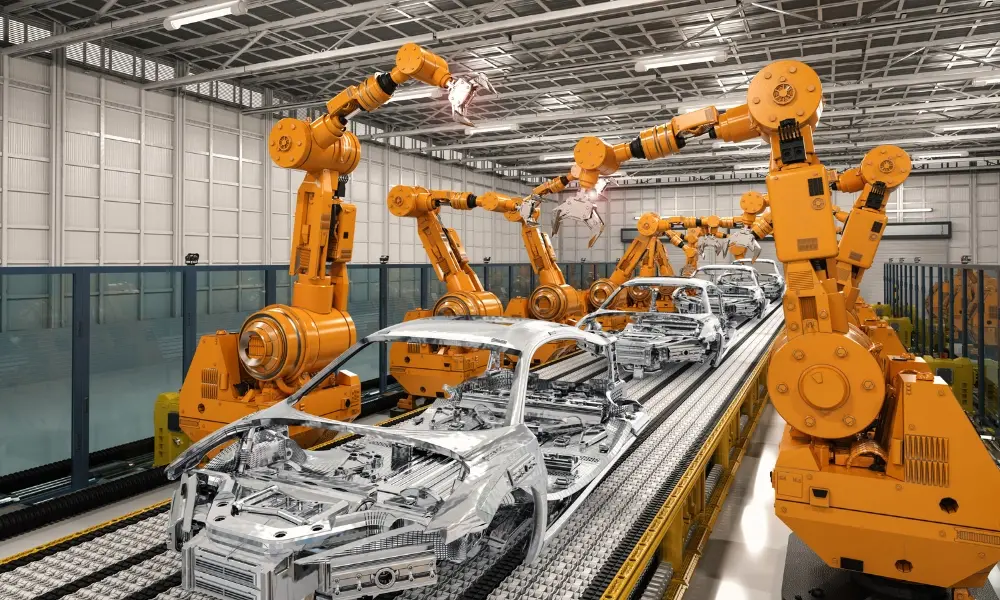
A robotic arm is a device designed to perform tasks quickly, accurately, and efficiently. It is typically powered by motors and consists of multiple joints, rotating components, and control mechanisms that enable the automation of heavy or repetitive processes with high speed and precision. As a result, robotic arms are particularly useful in industries such as manufacturing, mechanical processing, fabrication, and assembly.
In factories, robotic arms are used to automate repetitive tasks, such as spraying paint onto equipment or components. In warehouses, robotic systems assist in sorting and organizing goods from conveyor belts for order processing. In agriculture, robotic arms can harvest ripe fruit and carefully place it into storage trays with precision.
With advancements in technology and decreasing production costs of robotic components, robotic arms and industrial robots have become more accessible and widely adopted across various sectors, from large-scale factories to small and medium-sized enterprises.
2. Characteristics of robotic arms
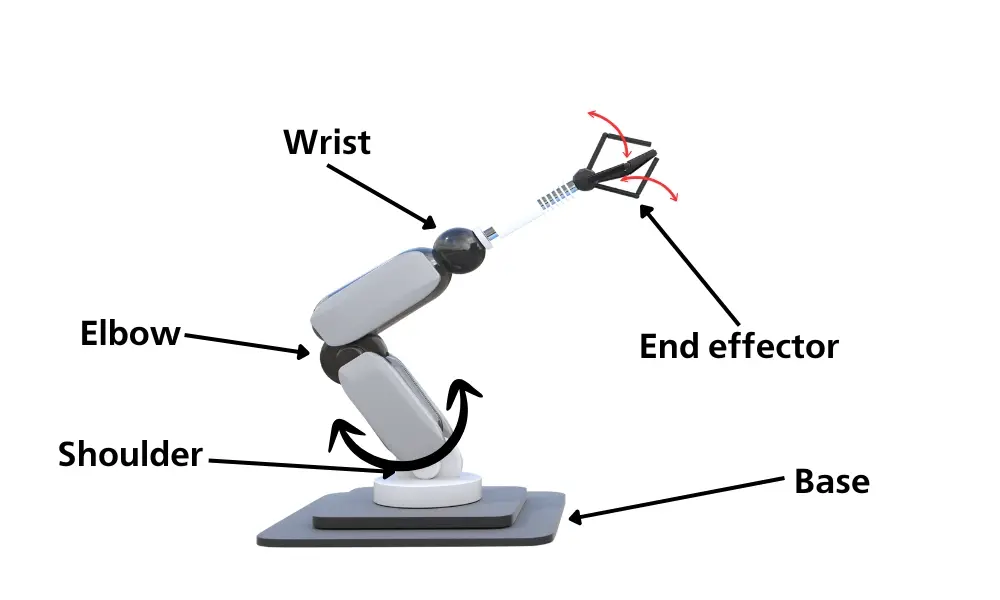
2.1 Structure of robotic arms
A robotic arm consists of various components that work in harmony to ensure precise and efficient operation, contributing to increased productivity in manufacturing:
- Controller: Acts as the brain of the robotic arm, processing and coordinating all activities. It can be programmed for autonomous operation or manual control.
- Arm: Comprises three main sections - shoulder, elbow, and wrist. The shoulder serves as the base, usually connected to the controller, and can move forward, backward, or rotate. The elbow, positioned in the middle, allows the upper and lower arm sections to move independently. The wrist, located at the end of the arm, connects to the end effector to execute the final operation.
- End effector: Functions as the hand of the robotic arm. It typically has two or three gripping fingers that can open and close flexibly as needed. Some models feature a rotating capability at the wrist, enhancing material handling and manipulation.
- Actuators: Drive the movement of the robotic arm’s joints.
- Sensors: Modern robotic arms are often equipped with sensors to enhance interaction with their surroundings. For example, sensors help robots avoid collisions with other robots in the same workspace or adjust their gripping force to prevent damage to fragile materials.
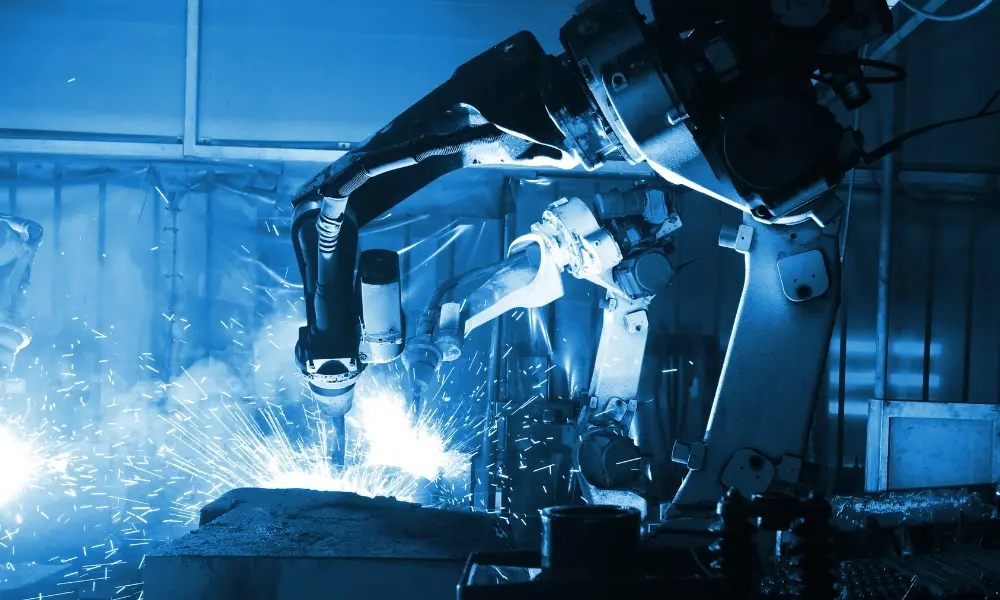
Welding robots
2.2 Operating principle of robotic arms
Industrial robotic arms execute tasks repeatedly according to pre-programmed instructions. Below is an overview of how they operate:
- Task programming: The first step is to define the task the robot needs to perform. Engineers create a program that specifies the robotic arm’s movements, speed, and actions of the end effector.
- Control system: The program is loaded into the robot’s controller, which functions as the central processing unit. This specialized computer deciphers the instructions and sends commands to various components of the robotic arm.
- Motion execution: The controller transmits signals to the motors at each joint of the robotic arm. Depending on the size and operational requirements, the robot may use electric, hydraulic, or pneumatic motors to generate the necessary movement force. As the motors activate, the joints rotate according to the programmed instructions, ensuring precise arm movement.
- Feedback and adjustment: The robotic arm is equipped with sensors that monitor its position and motion in real time. If any deviation from the programmed path is detected, the controller immediately adjusts the motor signals to correct the movement. This feedback loop ensures the robot operates with high accuracy and stability.
- End effector operations: The end effector at the tip of the robotic arm performs programmed actions such as picking and placing objects, welding, painting, assembling components, drilling, grinding, or polishing.
3. Types of industrial robotic arms
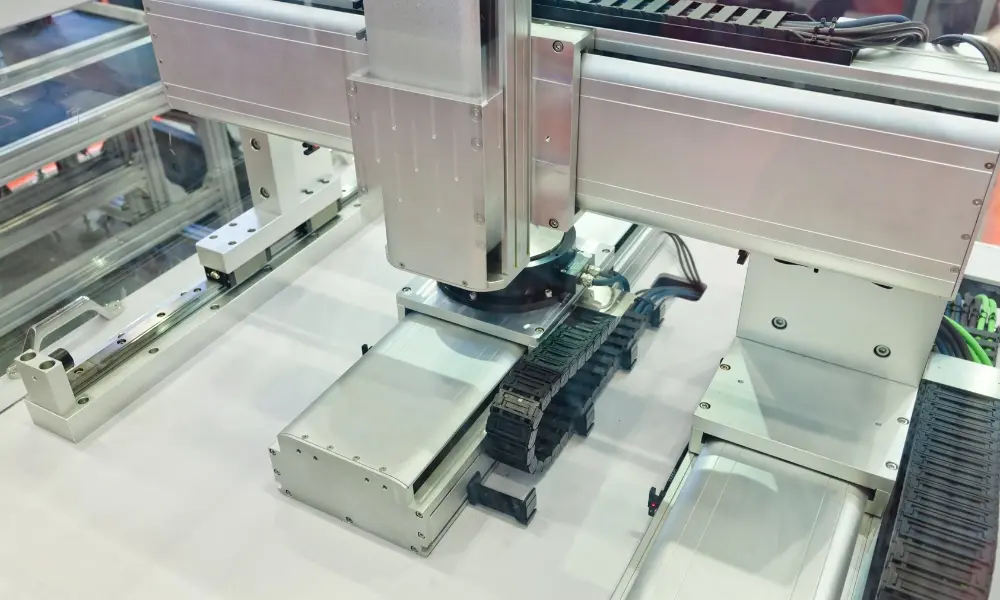
Cartesian robot arms
There are various types of robotic arms, each designed with specific functions and characteristics suited for different industries. Below are some of the most common types:
3.1 Cartesian robots (linear robots)
These robots operate within a Cartesian coordinate system (X, Y, Z) and are often referred to as rectangular or three-axis robots. Cartesian robotic arms move tools or attachments through linear motion to change positions in three dimensions. They achieve this using different types of motors and linear actuators.
3.2 Cylindrical robots
Cylindrical robotic arms operate within a cylindrical coordinate system, meaning their programmed movements occur within a cylindrical workspace (moving up, down, and rotating around an axis). Their rotary and sliding joints allow both linear and rotational movement, making them well-suited for assembly tasks, spot welding, and machine tool handling.
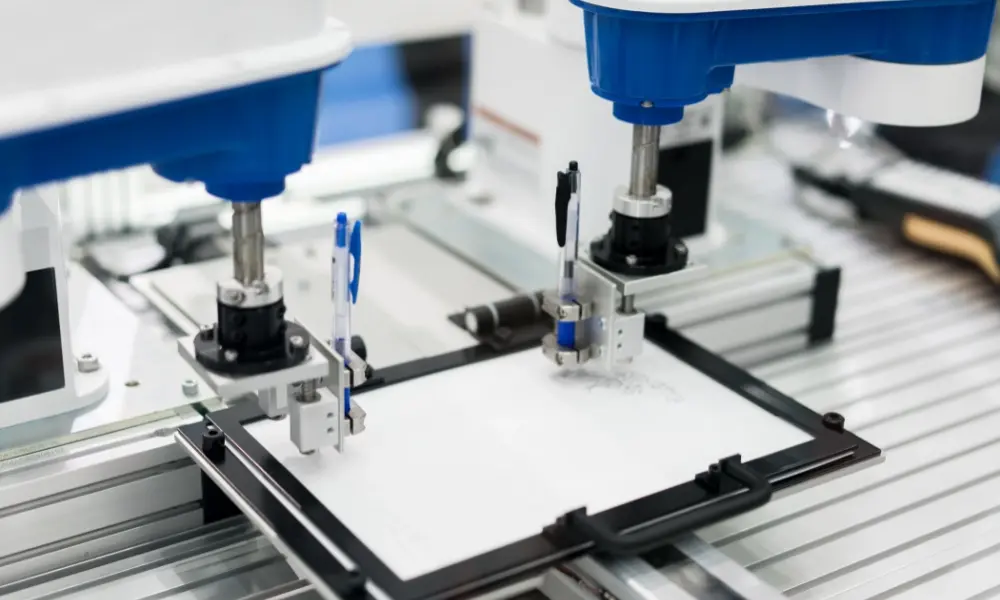
SCARA robot arms
3.3 Collaborative robots (cobots)
Collaborative robots are designed to work safely alongside human workers. Unlike traditional industrial robots, cobots prioritize safety, featuring rounded edges, force limitations, and lower payload capacities. Most cobots are equipped with multiple sensors to prevent accidents with human operators and include built-in safety protocols that shut down the system if unintended interactions occur.
3.4 SCARA robots
SCARA (Selective Compliance Assembly Robot Arm) robots are known for their ability to maintain rigidity along certain axes while remaining flexible in others. Due to their selective compliance, SCARA robots are widely used in high-precision manufacturing and assembly lines.
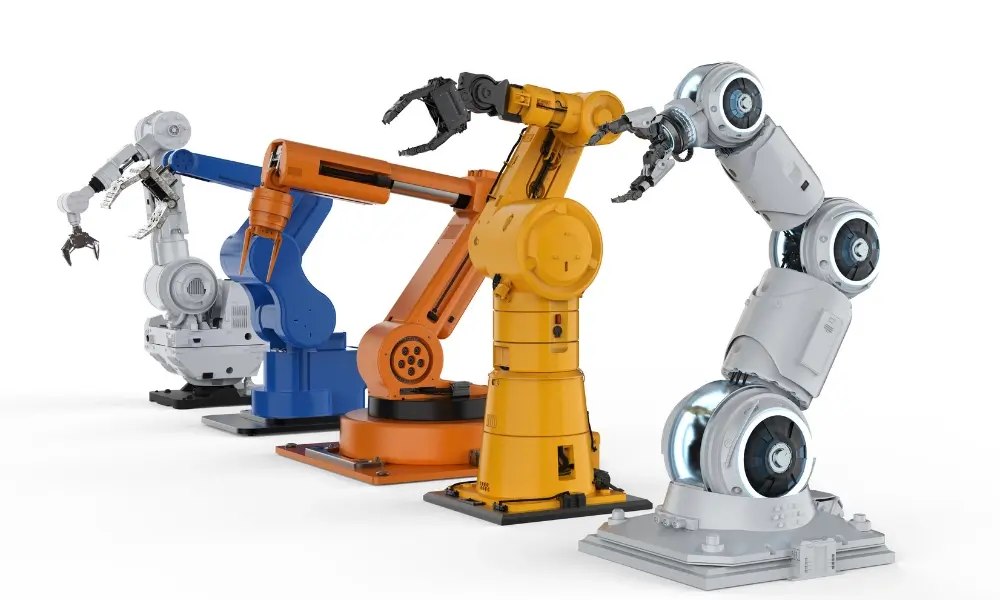
Articulated robotic arms
3.5 Spherical robots (polar robots)
These robots operate within a spherical workspace. They achieve this through a combination of a rotating base joint, two rotary joints, and one linear joint. The spherical robotic arm has a swiveling joint connecting it to the base, allowing it to reach areas that cylindrical robots cannot. Typical applications include machine tool operation, spot welding, die casting, and arc welding.
3.6 Articulated robotic arms
Thanks to their mechanical advantages, articulated robotic arms are the most common and durable type of industrial robots, making them widely used in manufacturing. Their precise movements, extensive range of rotation, and ability to extend linearly give them a distinct advantage.
Six-axis robots are the most popular type of articulated robotic arms and the most commonly used industrial robots today. Their versatility makes them ideal for a wide range of applications, and they are one of the most recognizable industrial robotic arms.
4. Applications of robotic arms in industry
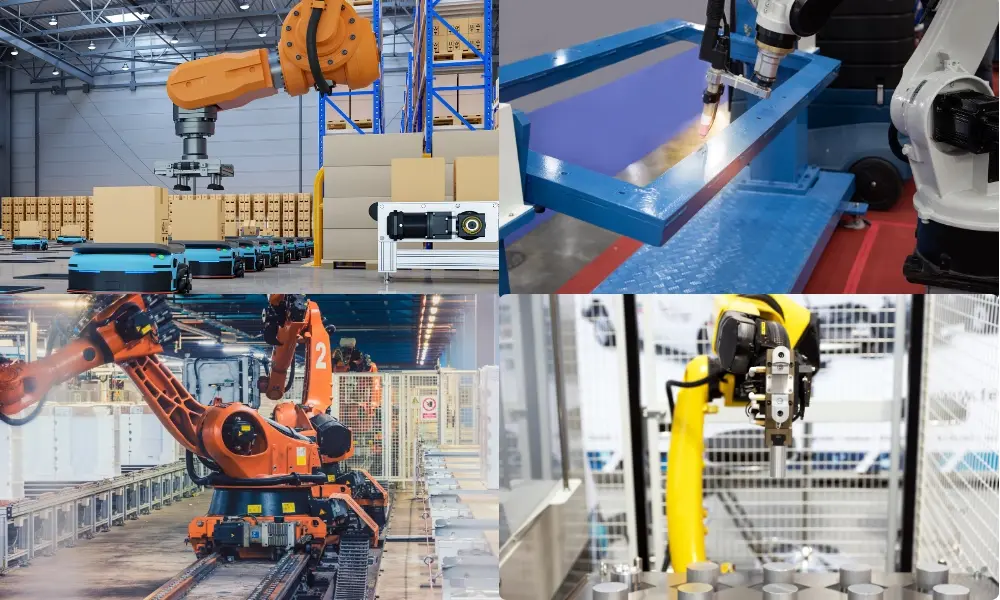
One of the key advantages of robotic arms is their versatility in supporting a wide range of applications, from simple tasks to highly complex operations in both safe and extreme environments. Below are some common ways manufacturers utilize robotic arms today:
- Palletizing: Robotic arms can automate the process of stacking goods or products onto pallets. Automating this process improves accuracy, reduces labor costs, and increases efficiency.
- Material handling: Robotic arms used for material handling contribute to safer and more efficient warehouses by ensuring goods and materials are properly stored, easy to locate, and accurately transported. Automating these processes speeds up delivery times and boosts productivity.
- Welding: Welding is a task that robotic arms can perform in advanced industrial environments such as automobile manufacturing. Since welding quality significantly impacts product reliability, robotic arms equipped with vision systems and AI enhance precision and consistency while conducting real-time quality inspections.
- Inspection: Quality control inspections are often performed at the end of production lines, delaying defect detection. By equipping robots with vision systems and AI, businesses can benefit from real-time inspections, minimizing waste and reducing downtime.
- Pick and place: Pick-and-place robots are widely used in modern manufacturing and logistics. Equipped with advanced computer vision systems, they can identify, grasp, and transfer objects from one location to another with speed and efficiency.
5. The role of cables in robotic arms
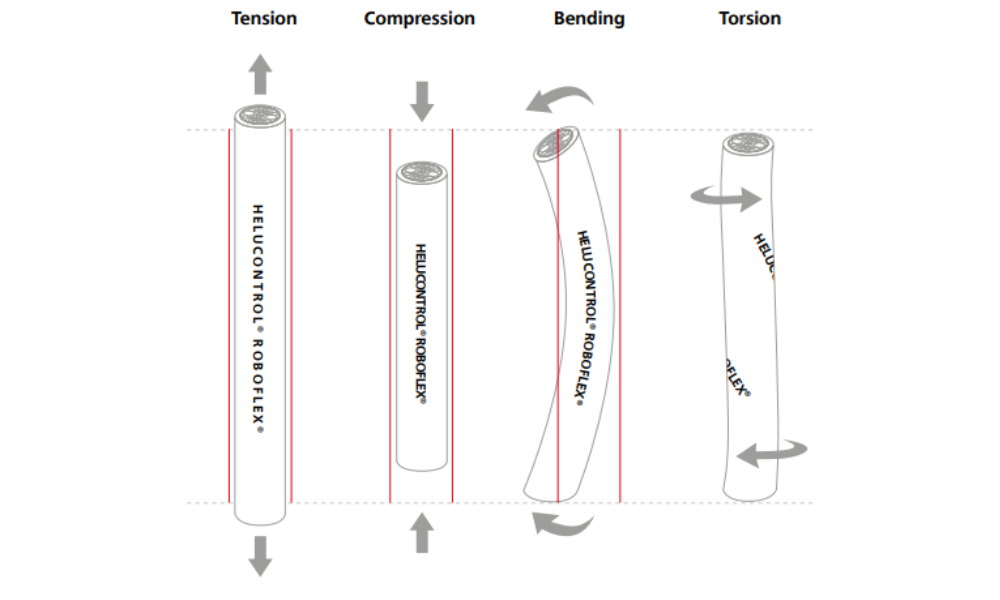
5.1 Features of cables used in robotic arms
The operating environment of robotic arms presents unique challenges for electrical cables and cable accessories. To ensure optimal performance and efficiency, robotic cables must meet the following requirements:
- Rapid acceleration and deceleration
- Resistance to mechanical stress: Robotic cables must endure twisting, bending, tensile loads, and other dynamic movements.
- Durability in extreme conditions: These cables must perform reliably in environments with extreme temperatures, dust, moisture, and exposure to chemicals.
- Resistance to mechanical, chemical, and thermal stress
5.2 HELUKABEL ROBOFLEX® cables for robotic applications
HELUKABEL offers a comprehensive range of cables for robotic arm applications, including control and motor cables in various sizes, hybrid cables, and cables for sensors, data transmission, networking, and bus systems.
ROBOFLEX® is a specialized cable series designed specifically for robotic applications. Key features include: UL/CSA certification, temperature resistance up to 90°C, halogen-free composition…
ROBOFLEX® cables | Nominal voltage | Torsion load/ cycle | Bending cycles |
HELUDATA® ROBOFLEX® PUR UL/CSA | UL (AWM) 300V | 5 Mio. at +/- 360°/m 10 Mio. at +/- 180°/m | 10 million |
HELUDATA® ROBOFLEX®-D PUR UL/CSA | 5 Mio. at +/- 180°/m | 5 million | |
HELUDATA® ROBOFLEX®-PAIR-D PUR UL/CSA | 5 Mio. at +/- 180°/m | 5 million | |
HELUCONTROL® ROBOFLEX® PUR UL/CSA | UL (AWM) 600V | 5 Mio. at +/- 360°/m; 10 Mio. at +/- 180°/m | 10 million |
HELUCONTROL® ROBOFLEX® -D PUR UL/CSA | 5 Mio. at +/- 180°/m | 5 million | |
HELUPOWER® ROBOFLEX® PUR UL/CSA | UL (AWM) 1000V | 5 Mio. at +/- 360°/m; 10 Mio. at +/- 180°/m | 10 million |
HELUPOWER® ROBOFLEX®-D PUR UL/CSA | 5 Mio. at +/- 180°/m | 5 million | |
HELUPOWER® ROBOFLEX® HYBRID PUR UL/CSA | UL (AWM) 1000V | 5 Mio. at +/- 360°/m; 10 Mio. at +/- 180°/m | 10 million |
HELUPOWER® ROBOFLEX®-D HYBRID PUR UL/CSA | 5 Mio. at +/- 180°/m | 5 million | |
HELUDATA® ROBOFLEX®-recycle PUR UL/CSA | UL (AWM) 300V | Up to 10 Mio. at +/- 360°/m | Up to 10 million |
5.3 Ethernet cables and bus cables for robotic applications
Besides the ROBOFLEX® cable series, several other cables are also used for robotic arms, including:
Type of cable | Features |
PROFInet Type R, torsion, PUR, Cat. 5e | Excellent transmission characteristics, double shielding |
100 T Tordierflex, SF/UTP, Cat. 5 | Outstanding performance / reserve capacity, after extreme conditions |
600 S PROFInet torsion, SF/FTP, Cat. 7 | Torsion design with special shield construction, torsion-optimised for use in robots |
Profibus L2, torsion, highly flexible, PUR + PVC | Torsion structure allows torque |
If you still have any concerns or questions, don't hesitate to reach out to HELUKABEL Vietnam's engineering team promptly for detailed assistance.
HELUKABEL® Vietnam
Address | 905, Nguyen Kiem Street, Ward 3, Go Vap District, Ho Chi Minh City 700000, Vietnam |
info@helukabel.com.vn | |
Hotline | +84 28 77755578 |
Website | www.helukabel.com.vn |
Discover our products and place orders | Tiki | Product finder |
Follow us on | Facebook | LinkedIn | Instagram | Youtube | Zalo | WhatsApp | Tiktok | Spotify |