Benefits of using VFD control and motor supply cables
VFD control and motor supply cables are designed to transmit electrical power to variable frequency AC drive systems to control the speed and torque of electric motors.
1. A glance at control and power cables for VFD applications
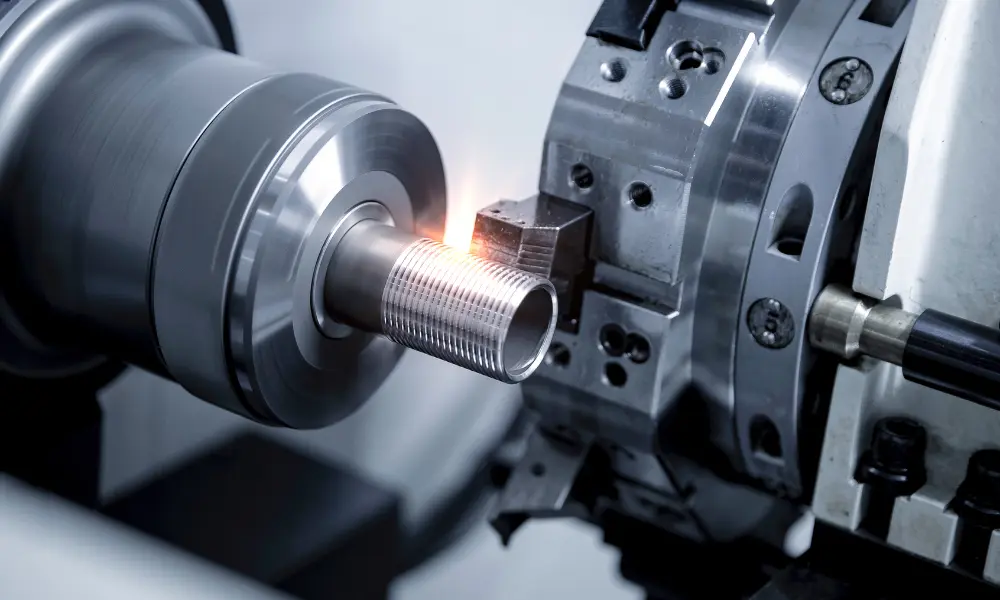
1.1 What is VFD?
Since the invention of electricity, electric cables have been used to power light bulbs and simple appliances, which are primarily resistive loads. However, new motor products have created challenges for the cable industry, with power requirements of up to 600 V, higher than normal starting currents, locked rotor pulses, speed variations, and encoder/decoder controls. A major change has been the development of precision motor control through variable frequency drives (VFD) and servo motors, necessitating significant changes in control cables to power and ensure motor performance.
A Variable Frequency Drive (VFD) is an electric motor controller that varies the frequency and voltage supplied to the electric motor. Other names for VFDs include variable speed drives, AC drives, and AC current regulators. Frequency (or hertz) is directly related to the speed of the motor (RPM – revolutions per minute). In other words, the higher the frequency, the faster the RPM. If an application does not require the electric motor to run at full speed, a VFD can be used to reduce the frequency and voltage to meet the load requirements of the electric motor. As the motor speed requirements of the application change, a VFD can simply increase or decrease the speed of the motor to meet the speed requirement.
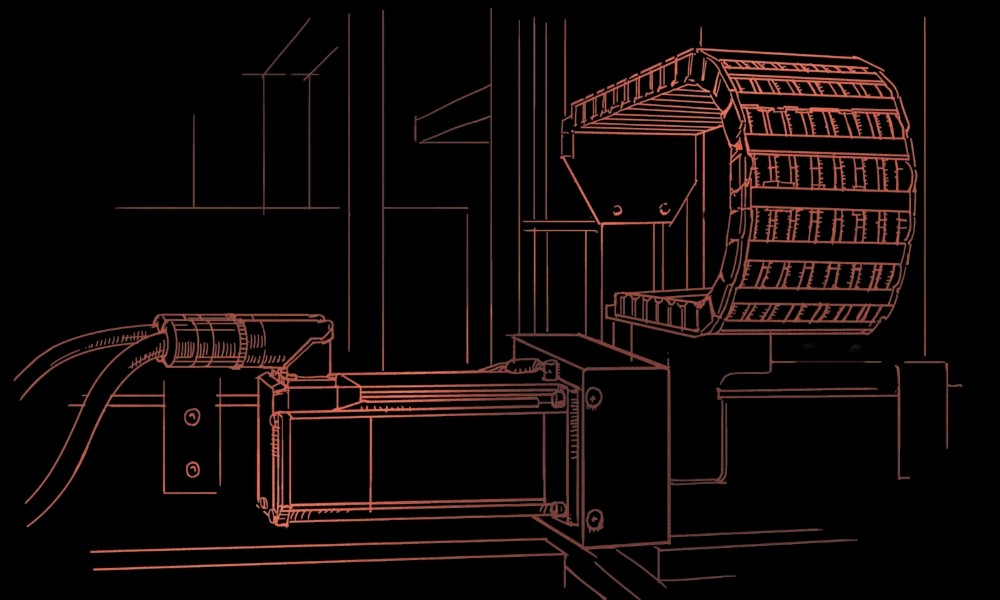
1.2 Control and power cables for VFD applications
VFD control and power cables, or variable frequency drive (VFD) cables, transmit power to variable frequency AC drive systems. These cables are designed for applications with harsh operating conditions, such as voltage spikes, high noise levels, and adverse environmental conditions. They are used in various industries, including nuclear power, industrial automation, power generation, solar energy, and wind energy.
VFD control cables are built to be highly efficient and can help prevent damage to motors, bearings, drives, and other related equipment. They are also designed to handle the fluctuating power demands of motors and other equipment, ensuring optimal performance for VFD drives.
2. Benefits of using VFD cables
VFD cables play an important role in extending the life cycle of VFD motors. The reason is that this type of cable has the following advantages:
2.1 VFD cables address high and low frequency interference issues with proper shielding.
The anti-interference layer is crucial in preventing systems from interfering with each other. Traditional THHN (Thermoplastic High Heat Resistant Nylon) braided nylon cables and most conventional control/tray cables are either unshielded or use aluminum shielding.
HELUKABEL VFD control and power cables, however, are constructed using advanced shielding techniques. They utilize aluminum foil (providing 100% coverage) combined with a tinned copper braid (providing 85% coverage), or triple shielding that includes semi-conducting fleece, aluminum foil, and tightly braid shielding (providing 80% coverage). Properly shielded control cables will prevent the VFD system from emitting electrical noise, which can interfere with surrounding networks, measuring equipment, wireless communications, and industrial equipment.
2.2 VFD cables can withstand voltage spike and reflective wave phenomena (RWP)
Control cables resist voltage spikes through their insulation material and wall thickness. HELUKABEL ‘s VFD control cables use XLPE insulation, which has much lower capacitance compared to the PVC insulation used in THHN cables and general control/tray cables. This is especially important in humid environments, as PVC is more prone to absorbing moisture, resulting in insulation that is less effective than XLPE. The wall thickness of VFD control cables is generally greater, allowing them to withstand voltage spikes significantly better.
Between the VFD and the motor, a significant amount of electrical noise is experienced in the form of voltage spikes, reflected waves, charging currents, common mode voltages, and RWP/electromagnetic interference (EMI). These issues can result in voltages that are twice the supply voltage. In the case of non-VFD control cables, this can lead to insulation breakdown and cable failure. Non-VFD cables also allow common mode voltage to pass through the ground of the VFD motor and equipment, causing damage to both the motor and the equipment.
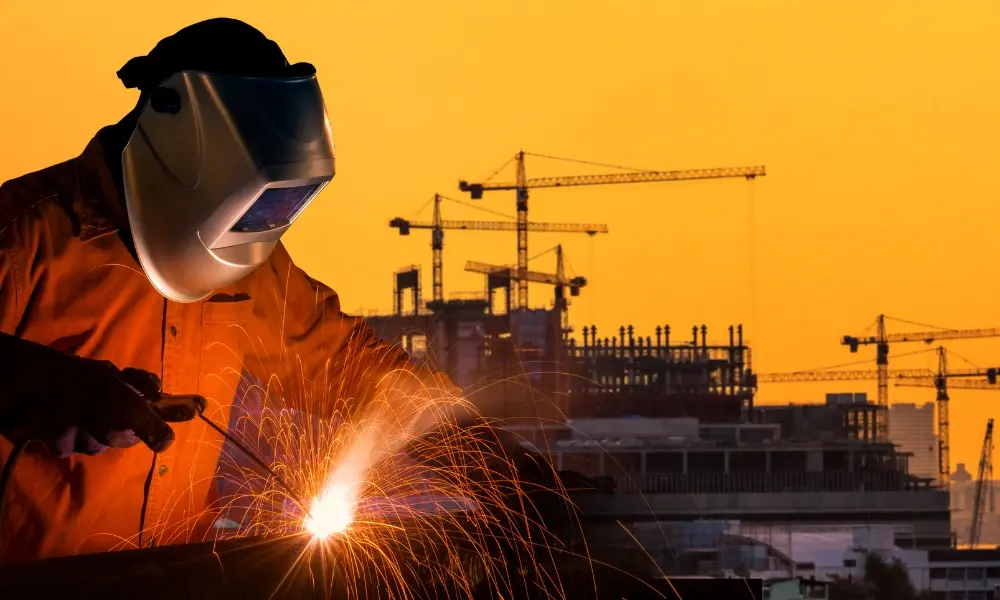
2.3 VFD cables are resistant to high temperatures
The insulation of control cables plays a significant role in how the cable reacts to thermal stress. Thermosetting insulation will not melt or drip at high temperatures like the thermoplastic insulation found in THHN cables and general control/tray cables. If thermoplastic insulation is used, there is a risk that the material will melt, drip or deform, reducing the insulation properties and potentially causing damage to critical equipment/machinery.
3. HELUKABEL’s control and power cables for VFD applications
HELUKABEL's control and power cables for VFD applications include:
Product | Description |
TOPFLEX® 600 VFD | EMC-preferred type, flexible motor power supply cable, oil resistant, NFPA 79 |
TOPFLEX® 650 VFD | EMC-preferred type, flexible motor power supply cable with control cores, oil resistant, NFPA 79 |
TOPFLEX® 1000 VFD | EMC-preferred type, motor power supply cable, NFPA 79 |
TOPSERV® 600 VFD | Oil Res I/II, exposed run: TC-ER, PLTC-ER, ITC-ER, NFPA 79, EMC-preferred type |
TOPSERV® 650 VFD | Oil Res I/II, exposed run: TC-ER, PLTC-ER, ITC-ER, NFPA 79, EMC-preferred type |
3.1 TOPFLEX® 600 VFD and TOPFLEX® 650 VFD
TOPFLEX® 600 VFD (PVC outer sheath) and TOPFLEX® 650 VFD (TPE outer sheath) exhibit the following characteristics:
TOPFLEX® 600 VFD | TOPFLEX® 650 VFD | |
Operating temperature | -25°C to +90°C | -25°C to +105°C |
Nominal voltage | TC 600 V WTTC 1000 V | |
Minimum bending radius | 6x Outer-Ø (flexing) | |
Structure of cable |
|
These two cables offer excellent oil resistance for modern servo motors. The double shielding, consisting of special aluminum foil (100% coverage) and tinned copper braid (approximately 85% coverage), provides effective protection against electrical noise and damage. The cables comply with NFPA 79 and are approved for open, unprotected installation on cable trays and from cable trays to machines. The special TPE and PVC outer sheaths are extremely resistant to oil, coolants, and solvents, making them the perfect solution for industrial applications with open installations, installations in pipes, and underground installations.
3.2 TOPFLEX® 1000 VFD control and power cables
Operating temperature |
|
Nominal voltage | UL 1277 - TC 600 V UL 2277 - WTTC 1000 V |
Minimum bending radius | 15x cable Ø (flexing) 7,5x cable Ø (fixed installation) |
Properties and applications of the cables |
|
3.3 TOPSERV® 600 VFD and TOPSERV® 650 VFD
TOPSERV® 600 VFD | TOPSERV® 650 VFD | |
Operating temperature | Flexing: +5°C to +50°C Fixed installation: -40°C to +105°C UL (TC) +90°C | |
Nominal voltage | UL (TC) AC 600 V UL (WTTC) AC 1000 V CIC-TC AC 600 V | |
Minimum bending radius | 10x cable Ø (flexing) 5x cable Ø (fixed installation) | |
Properties and applications of the cables |
|
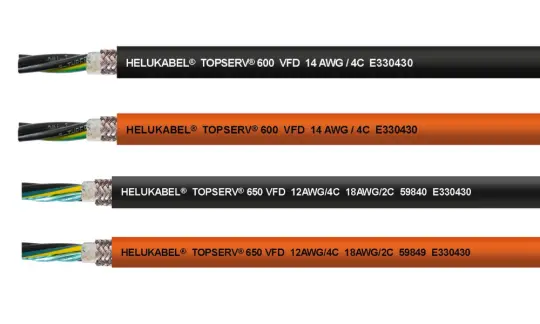
If you still have any concerns or questions, don't hesitate to reach out to HELUKABEL Vietnam's engineering team promptly for detailed assistance.
HELUKABEL® Vietnam
905, Nguyen Kiem Street, Ward 3, Go Vap District, Ho Chi Minh City 700000, Vietnam
Tel. +84 28 77755578 | info@helukabel.com.vn | www.helukabel.com.vn